Practical Steps to Improve Manufacturing Logistics:
Assessment, Measurement and Problem Solving
Continuous Improvement in Manufacturing & Logistics
In my experience, manufacturing logistics and fulfillment operations often face similar challenges. Largely because they have the same goal: -to run as efficiently as possible. Optimizing operations helps deliver actual measurable benefits—reducing costs, fewer delivery errors, and improving employee morale.
When seeking optimization opportunities within logistics environments, the number of potential starting points can be overwhelming. In this article I provide a systematic approach to continuous improvement by focusing on three critical components: initial assessment, implementing effective KPI measurements, and applying practical problem-solving techniques when KPIs fall outside acceptable parameters.
Where to Start
Choosing where to begin your improvement journey is important, but the most crucial step is simply to start. You can prioritize based on:
- Account-specific activities with performance issues
- Warehouse segments experiencing delays or incidents
- Areas with recurring problems or bottlenecks
Begin by categorizing the different operational areas that require evaluation. Prioritize them based on impact and urgency, then methodically work through your list.
Our Scenario
To illustrate our approach, we'll examine a specific case that keeps the scope focused and manageable. We'll walk through the assessment, measurement, and problem-solving process for a raw materials fulfillment operation at one of our facilities supporting a semiconductor manufacturer.
While this operation occupies only a small section of one of our Austin warehouses, it serves as an excellent example for demonstrating our improvement methodology.
Initial Assessment
An effective assessment doesn't require weeks or even days. A focused 4-8 hour review can provide comprehensive insights into operational performance. In many cases, daily Gemba Walks are enough to identify significant improvement opportunities.
For our case’s fulfillment operation, I spent one day examining building layout, operational flow, picking processes, safety considerations, and other key factors.
For this article, we'll concentrate on two critical assessment components: building layout and order picking flow. Key aspects examined included:
- Material flow mapping: Tracking the movement of products from receiving to storage to picking to shipping, utilizing a spaghetti diagram to visualize inefficient movement patterns.
- Movement analysis: Measuring the actual steps required to fulfill common orders, providing quantitative data on travel distance per operation or task.
Spaghetti Diagram Example
Process Cycle Time Analysis Example
These assessment elements, while just a subset of a complete evaluation, revealed significant improvement opportunities for our case.
Practical Problem Solving (Part 1)
With our assessment data on pick flow and travel distance, we next apply structured problem-solving methods to find improvements. This is commonly called Practical Problem Solving (PPS) and it typically involves standardized processes, templates, and frameworks to address issues and define expected outcomes.
For the excessive travel distance identified in our assessment, we utilized our Travel Distance Savings Framework to:
- Document current state: Calculate total daily travel distance by multiplying average distance per order by orders per day.
- Quantify cost impact: Apply hourly labor costs to time spent traveling to determine total cost associated with current movement patterns.
- Design improved state: By analyzing picking patterns and identifying frequently picked items, we redesigned the warehouse layout to optimize product placement. Our solution reduced travel distance by 40% per order.
- Calculate savings potential: Using the same template, we maintained the same order volume but reduced the distance per order, revealing significant hard and soft savings when projected annually.
KPIs
For each improvement initiative, we want appropriate performance metrics. Effective KPIs must genuinely measure what they claim to measure. A metric that fluctuates without accurately reflecting performance provides no value.
For our travel distance improvement, we implemented two complementary KPIs:
- Order Cycle Time: Measuring the duration from when an associate begins processing an order until it's ready for shipment. This directly tracks the efficiency of preparing each order.
- Pick Accuracy: Tracking the percentage of orders fulfilled without errors. This ensures that speed improvements, or other factors, don't come at the expense of quality.
These paired metrics allow us to confirm that our new layout truly delivers better results while maintaining order integrity.
Practical Problem Solving (Part 2)
Even well-designed processes will eventually experience performance issues. When KPIs fall outside acceptable parameters, proactive management is critical—not just acknowledging the problem but systematically addressing it.
In our case, after implementing our new layout, Order Cycle Time remained within acceptable parameters, but Pick Accuracy declined by 12%. To address this, we employed the A3 Project Management methodology—a structured problem-solving approach that:
- Documents the problem: We identified that similar-looking parts with similar identification numbers were being confused during picking.
- Analyzes root causes: Through direct observation and data analysis, we determined that poor lighting in storage areas and minimal visual differentiation between packaging contributed to the errors.
- Develops countermeasures: Our solution included enhanced lighting in picking areas, color-coded storage locations for similar items, and modified labeling with visual indicators to distinguish similar parts.
- Implements and validates: After implementing these changes, we monitored Pick Accuracy for three weeks, confirming a return to acceptable levels.
The A3 framework provided a concise, logical narrative that enabled team alignment and focused problem-solving.
To see an example of an A3 storyboard, see HERE.
Conclusion
In my experience, continuous improvement in logistics operations requires a systematic approach. These are some of the actions to keep in mind:
- Regular assessments of operational areas based on management priorities, conducted on a scheduled cadence to identify issues that may not be captured by existing KPIs alone.
- Implementation of targeted KPIs that accurately measure performance in critical areas.
- Proactive management of KPI deviations through structured problem-solving methodologies.
This cyclical process—assess, measure, solve, repeat— helps creates a foundation for ongoing optimization that has helped my operations drives both improvements and competitive advantage.
About
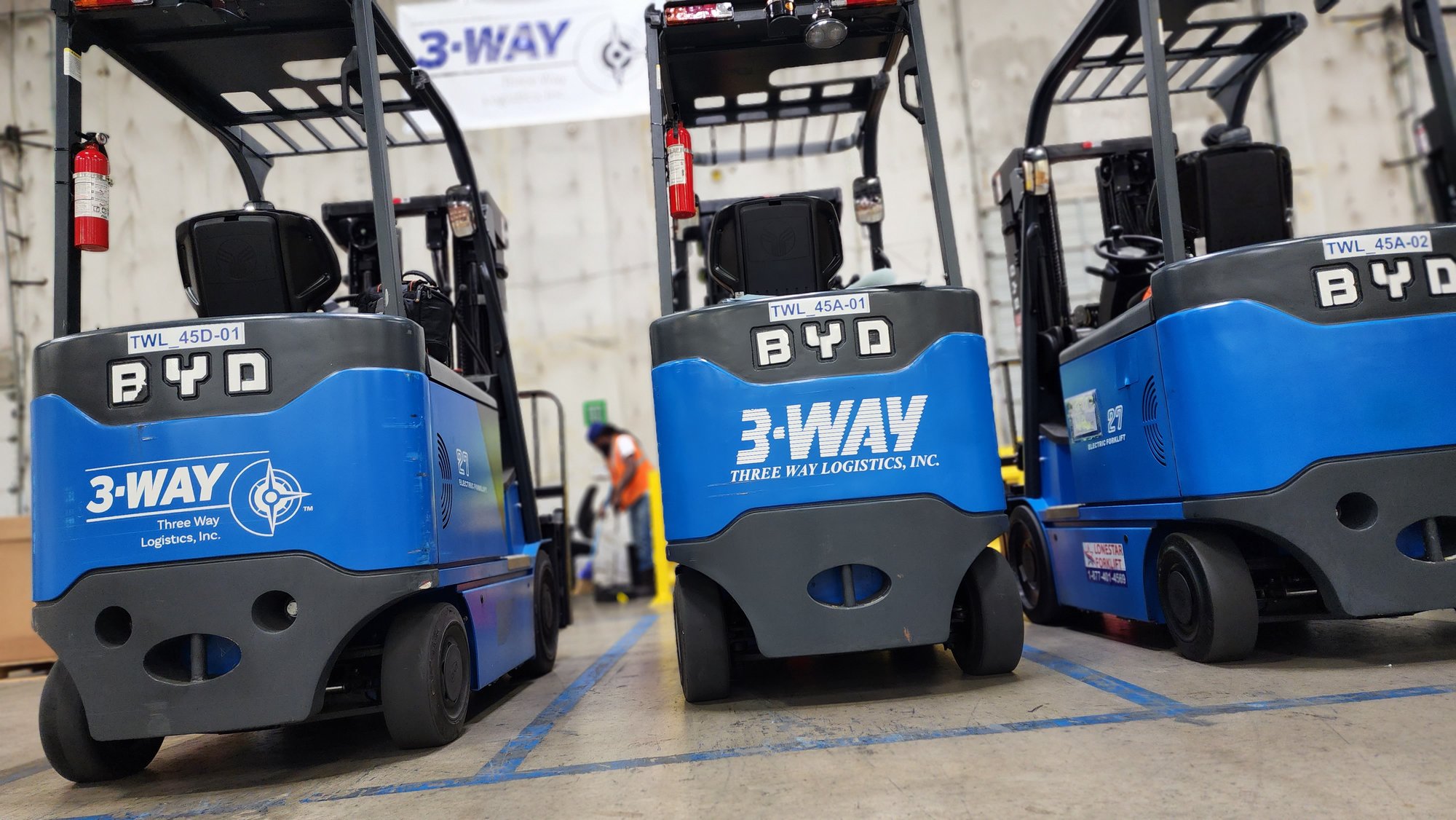
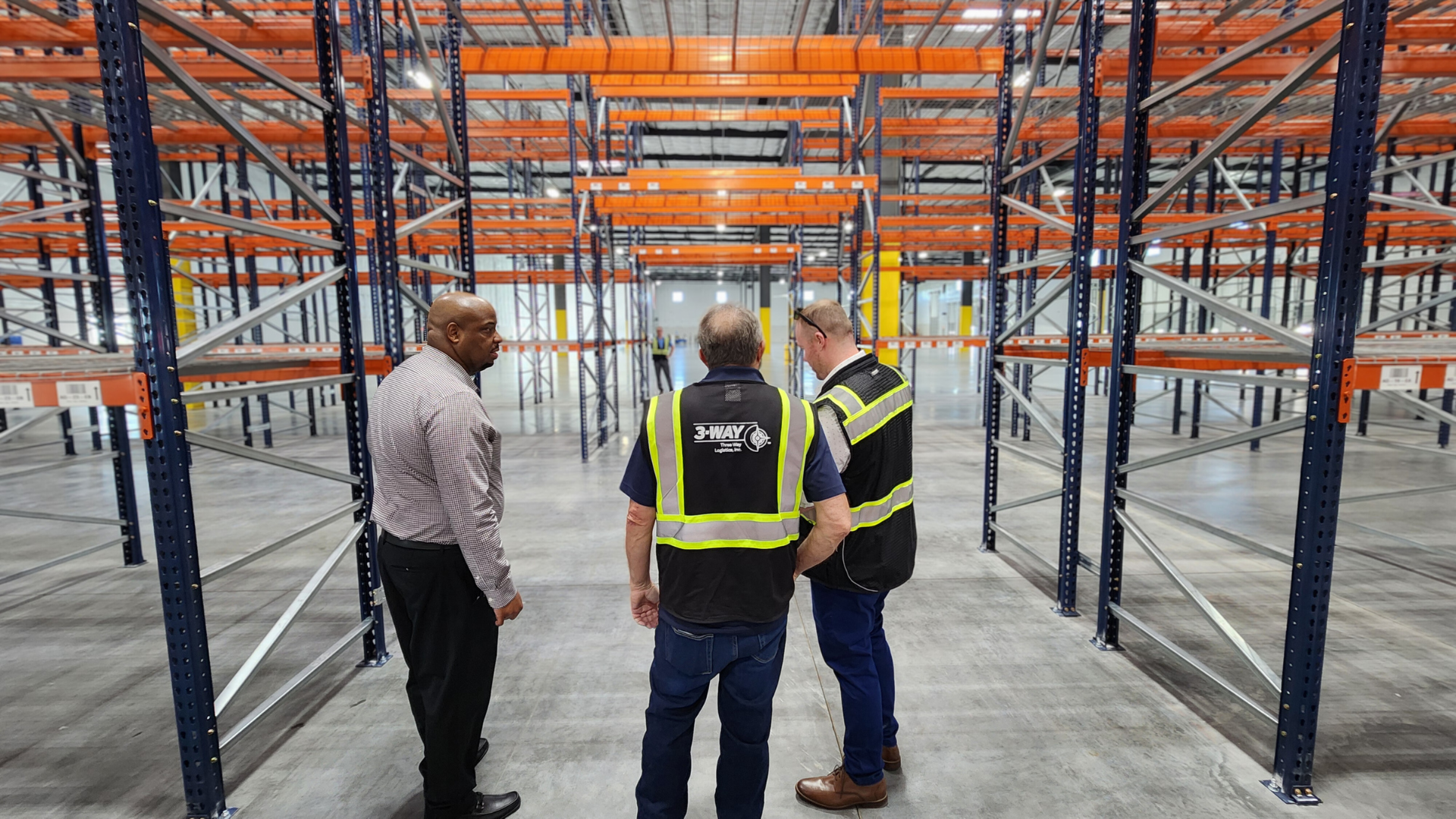
.png)